“Without standards, there can be no improvement.” – Taiichi Ohno, father of the Toyota Production System. While this is a relatively simple and straightforward remark, it represents a significant foundational piece for improvement initiatives.
Think about it – if every member of a team has a different way to complete a task, it’s likely there will be unnecessary variation in the results that add no value to the customer, client, or patient. And how can you improve a process if there isn’t one in place to improve in the first place?
Let’s use hand hygiene as an example of why a standardized process is useful. We know that having clean hands is important, but we also know that areas like your thumbs and between your fingers are consistently missed. Unless you have a clear set of steps that need to be completed, it’s easy to miss a step or two without noticing. Also, once everyone is completing the same steps, it’s easier for a team to look at the full process and see where it can be improved.
So how do you go about doing that? One way is through the use of a tool called a work standard.
Read on to learn what work standards are, how to write them, and how they can help set your team up for success in quality improvement initiatives.
Table of contents
- What is a work standard?
- Why you should document your processes into a work standard
- How to create a work standard
- Anatomy of a work standard
- How to implement a work standard
What is a work standard?
Simply put, a work standard is a clear set of instructions. They make it easy for a process to be done consistently, timely, and in a repeatable manner.
It sounds simple, but there is much more to it than simply creating a policy or how-to guide. Work standards are an integral part of quality improvement initiatives and there are a lot of differences that set them apart from other approaches.
Work standards are:
- A tool to capture best practices at a specific point in time
- Created by the team members doing the work
- A fluid document that is updated and improved to reflect new understandings of best practice
- A communication and knowledge translation tool
The goal of a work standard is to clearly and concisely frame a process as the steps required to complete a cycle of work.
It’s important to note that the people doing the work and who know the process should be the ones to improve the process and create the work standard. Of course, you should still work within the context of your organization and follow current guidelines and requirements, but generally speaking, the best way to create a work standard is to put people’s knowledge to work.

Why you should document processes into work standards
The purpose of work standards is to document processes that will consistently deliver a level of quality that a team needs. Teams create work standards to make sure everyone is completing the process the same way every time. That doesn’t mean work standards should be set in stone. Instead, they should be updated and improved to reflect new understandings of best practice.
It may seem like having a consistent process would lead to “mindless conformity,” but when routine processes are working as expected and in the most efficient way possible, you have the time and mental energy to focus your problem-solving skills on other areas that need more creativity and attention.
How to create a work standard
Now that we understand what a work standard is and why it is needed, it’s time to talk about how to write one.
Work standards are usually created at the end of improvement work. Improvement involves team working to understand a problem, identifying areas for improvement, then conducting Plan-Do-Study-Act cycles to improve the process. It is important to have a stable and reliable process in place before moving onto the next step of creating a work standard.

So you’ve made improvements and you now have a process that’s working well. What happens next?
Write it down and test it out, making sure you have thought through all of the steps. This will help your process become a repeatable action. Without documentation, it’s impossible to ensure that everyone is applying it consistently.
Sometimes people struggle with how to document their process and what level of detail should be included in a work standard. Our advice would be that a step should be anything that moves the work forward.
Back to our hand hygiene example, a step would be to squirt a quarter-sized amount of gel into the palm of your hand. It wouldn’t be to place your hand under the nozzle, then press down on the nozzle, then release the nozzle.
The step should include what needs to happen before moving onto the next step, and the level of detail should include anything that is job-specific to the how. So squirting gel into the palm of your hand would be a step because you couldn’t move onto the next step (covering your hands in the gel) without it, and the level of detail would be that you should use a quarter-sized amount.
We should also note that work standards can cascade. So, in a complex process, you might have one overarching work standard, but a particular step might have it’s own work standard that does into more detail.
Sometimes the terms “work standard” and “standard work” are used interchangeably, but they are two different things. The chart below explains the main differences between a work standard and standard work.
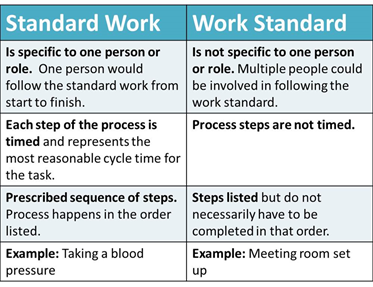
Regardless of which one you use, good standard work and work standards should:
- Be appropriately titled. It should be clear what the task is based on the title.
- Be written clearly. While standard work is not a replacement for training, it should be easy to follow for those doing the work.
- Be accessible. Standard work should be available to staff and managers as needed.
Anatomy of a work standard
By now you should understand what a work standard is and the process your team should go through to develop one. Now let’s talk about what one should look like.
At the top of a work standard, the first thing you will see listed is the name of the process and the operator(s) who will be performing the activity.
You will also notice, there is a section to include dates for when the work standard was initially prepared and when the last revision was made. As previously mentioned, work standards are not permanent and should be updated as best practices develop over time.
The work standard summary provides a brief description of the process that is being outlined. It usually states the starting and end points of the process.
Simple and straightforward steps should be included under the “Essential Tasks” section. The steps should only be listed in sequential order if that is required for the process to be effective. For example, you might have a work standard on setting up a meeting room. In this case, the order in which the steps are done is not important as long as all of the tasks are complete. It’s probably easier to follow the list, but it’s not essential.
Download the Hand Hygiene Work Standard Example.
How to implement a work standard
After working through PDSA cycles and documenting the steps of the process into a work standard, it’s then time to roll out the document.
Training staff on new work standards is an important piece of making the improvement stick. It’s also important to share the document with team members and save it in a location that is easily accessible.
And there you have it – your team now has a work standard! But your work is far from over, as quality improvement is never done. Now that your team has a work standard in place, you have a great launchpad for further improvements.
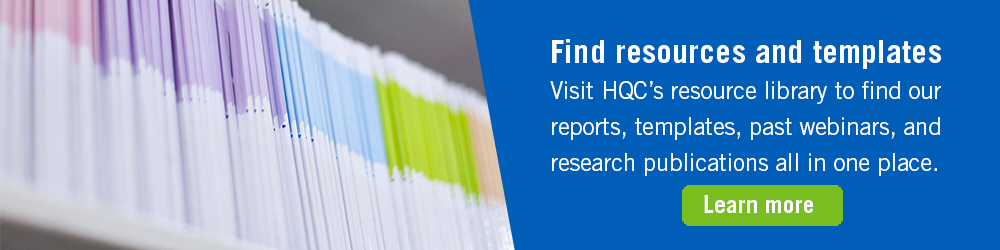