The Model for Improvement, improvement science, PDSA, process mapping – chances are you’ve heard at least a few of these terms in your work environment. But do you know what they are? These are all models, frameworks, tools, and techniques that fall under the umbrella term of quality improvement (QI).
But what exactly is QI?
Quality improvement (QI) is the framework used to systematically improve processes and systems.
But let’s not get too far ahead of ourselves. Before digging into the definition of QI and its applications, let’s first take a look at the concepts of quality and improvement separately.
Table of contents:
- What is quality?
- What is an improvement?
- What is quality improvement?
- The history of QI and modern applications
- The Model for Improvement
- The Toyota Production System
- The importance of quality improvement
- How to apply quality improvement in your work
What is quality?

Quality refers to the degree of excellence of something. The definitions of quality can vary across industries and it’s typically defined from the perspective of the end user.
Think of a time when you received exceptional service. It could have been at a restaurant, a gas station, a hotel, or an airport. What was it about that experience that made it stand out in your mind?
Within the automotive industry, quality can be defined by the customer buying a vehicle, and is often rated based on things like safety, reliability, gas mileage, and owner satisfaction. In the airline industry, quality is based on things like service from staff, ease of check-in, and seat comfort.
Consider for a moment how quality might be defined in the work you do. Who is the end user or customer of your processes? What type of output and outcomes are they looking for?
Within the health care sector, the definition of quality is based on six dimensions:
- Safe: Avoid harm to patients from care that is intended to help them
- Effective: Provide services based on scientific knowledge to all who could benefit and refrain from providing services to those not likely to benefit (avoid underuse and misuse of services, respectively)
- Patient-centred: Provide care that is respectful of and responsive to individual patient preferences, needs, and values to ensure that patient values guide all clinical decisions
- Timely: Reduce waits and sometimes harmful delays for both those who receive and those who give care
- Efficient: Avoid waste, including waste of equipment, supplies, ideas, and energy
- Equitable: Provide care that does not vary in quality because of personal characteristics such as gender, ethnicity, geographic location, and socioeconomic status
These six dimensions were originally laid out by out by the United States-based National Academy of Medicine (formerly the Institute of Medicine) in their 2001 report called Crossing the Quality Chasm. They highlight the complex nature of quality and that quality can be defined, measured, and improved upon.
Now that we have an idea of how quality is defined, let’s take a look at what is meant by the term improvement.
What is an improvement?

Improvements can be characterised as changes that make something faster, easier, more efficient, more effective, less expensive, safer, or a change that improves end-user satisfaction.
While there is a strong interplay between the concepts of improvement and change, it is important to note that all improvements require change, but not all changes result in improvements. Simply put, just because you change something, doesn’t mean it is actually improved.
Consider a change you could make in your daily life, such as altering your route to work. This may or may not result in improvement depending on what you are trying to accomplish and what your definition of success is. Do you want a shorter commute time? Are you taking a different route to avoid rush hour traffic?
For every change, it’s important to check in to identify whether or not it brought you closer to your end goal. If a change results in an improvement, it would:
- Alter how work or activity is done or the makeup of a product
- Produce a visible, positive difference in results
- Have lasting impact
Now that we have an understanding of the definitions of both quality and improvement, let’s bring it together and look at what quality improvement is.
What is quality improvement?

As previously mentioned, quality improvement (QI) is the framework used to systematically improve processes and systems. Just as it sounds, the goal of QI is to continuously look for ways to improve the quality of your organization’s outputs, which could be products, services, or outcomes.
But as we learned in the previous section, just because a change is made doesn’t mean it resulted in an improvement. That’s why QI is built on a foundation of measurement, goal-setting, and testing. It involves establishing standard processes to continuously monitor, assess, and improve processes towards a specific goal or outcome.
QI can be thought about as a combination of technical and behavioural skills. It’s comprised of tools, techniques, and frameworks for systematically improving processes and systems, but it’s also involves a shift in mindset.
Instead of adhering to the idea of “that’s the way we’ve always done things,” it is about being humble and curious and looking for opportunities to learn and improve.
This is a great opportunity to leverage any organizational performance data you may have on hand. What information do you have to tell you how your process or system is performing? What can you learn from your data about where to focus your improvement efforts?
The history of QI and modern applications

QI traces it roots back to the 1920s, and was first applied to manufacturing by pioneers like W. Edwards Deming, Walter Shewhart and Joseph Juran, widely regarded as the grandfathers of QI.
In this video, Dr. Mike Evans provides an overview of the history, goals and process of quality improvement in healthcare.
In healthcare, the goal of QI efforts is to improve the ways care is delivered to patients.
Like most industries, health care is made up of multiple processes, each with characteristics that can be measured, analyzed, controlled, and improved. QI is a continuous approach with the goal of achieving stable and predictable process results and improving outcomes for both patients and the system as a whole.
In industries outside of the health care sector, it’s important to define the end user of your process, and improve outcomes or outputs in service of them.
Consider the following questions to centre your improvement efforts:
- Who is the customer of this process?
- How would they define a quality experience and output of this process?
- What would success look like to them?
- What evidence do we have to help us understand how this process is currently working for them?
Two of the most widely used frameworks for quality improvement are the Model for Improvement and the Toyota Production System. Each of these models are applicable to and widely used across many industries, around the world. The next sections will explore these frameworks in further detail.
The Model for Improvement

The Model for Improvement was first developed by the Associates in Process Improvement and published in the first edition of The Improvement Guide in 1996. The model was later adopted by the Institute for Healthcare Improvement (IHI). It’s also referred to as the “IHI model” or the “PDSA method”.
The Model for Improvement is comprised of three fundamental questions, and an action cycle known as the Plan-Do-Study-Act (PDSA) Cycle.
The Model for Improvement is a framework for implementing the five fundamental principles of improvement:
- Knowing why you need to improve
- Having a feedback mechanism to tell you if the improvement is happening
- Developing an effective change that will result in improvement
- Testing a change before attempting to implement
- Knowing when and how to make the change permanent (implementing the change)
The Model for Improvement in centered on making small, incremental improvements over time using the PDSA Cycle, and tracking your progress towards a clearly defined aim. PDSA Cycles always start on a small scale, to minimize risk, and then are ramped up once you gain confidence that the change you are making is having the desired impact and resulting in what you set out to accomplish.
Recommended Resource:
- PDSA In Everyday Life (5 minute video)
The Toyota Production System

The Toyota Production System (TPS) – first developed and pioneered by the Toyota Motor Corporation for car manufacturing – is a production system based removing all waste to create the most efficient methods.
The concept of “waste” is defined as activities that do not add value to the product or service. TPS proposes seven different types of waste to tackle:
- Inventory: Having too much product on hand
- Waiting: Time on hand waiting for either people involved in the process, or the end-user
- Motion: People moving or walking more than is required to perform a task
- Transport: Moving supplies or equipment more than required
- Overproduction: Making more than is required
- Overprocessing: Doing more than is required to add value
- Defects: Mistakes happening at any step along the process, or in the end product or service
The TPS approach to improvement is rooted in establishing standardized processes and understanding those processes through data collection, to identify opportunities for improvement. The idea is to empower all staff to continuously look for ways to improve the workflow, every day.
Recommended Resources:
- Toyota Production System (Toyota website)
- Meals Per Hour: How TPS techniques were applied to the New York City Food Bank after Superstorm Sandy in 2012 (6 minute video)
The importance of quality improvement

Regardless of your industry, chances are your work involves people, processes, and problems. Problems can range from serious events like defects causing harm or death to people, and everyday annoyances, such as routinely not being able to find the supplies to do your job.
Problems are also rarely the result of any one person or process. Instead, they occur because processes exist within a complex system, and tend to not adapt over time to reflect changing business needs.
In most cases, working harder or faster will not solve your problems or improve your quality. But, working differently will.
QI is about continuously identifying and understanding problems, testing ideas to improve the problem, and measuring the results to see if they are taking us closer to where we want to be. In a rapidly-changing world, QI helps you adapt to changing needs, to stay relevant, and to better serve your end users.
QI yields the best results when it is approached as a “team sport.” While you can certainly practice QI skills on a small, individual scale (for example, you could organize your desk drawer, or develop a new filing system), the greatest gains are made when multiple perspectives are brought in and are focused on collectively solving a problem.
Full potential is reached when you’ve embedded a philosophy of QI in your organizational culture; Where everyone in your business comes to work every day with the understanding that they have two jobs to do: one is to do their job, and the other is to improve it.
How to apply quality improvement in your work
QI is highly scalable and widely applicable. It can range from testing the PDSA Cycle on a small scale to improve your morning routine, to tackling complex challenges such as improving access to community services.
But how do you get started on your learning journey? We invite you to start small. Download our PDSA Template, to help guide you through your improvement efforts.
Want to learn more? Take our two-hour self-guided course Introduction to Quality Improvement (see below for further details).
The Introduction to Quality Improvement Course is a two-hour self-guided course developed by the Health Quality Council. This course was developed with a healthcare audience in mind, however, the principles and tools covered are applicable to any sector or industry. This course if offered through the Moodle learning platform, and generates a certificate of completion for continuing education purposes.
Click here to learn more about the Introduction to Quality Improvement course.
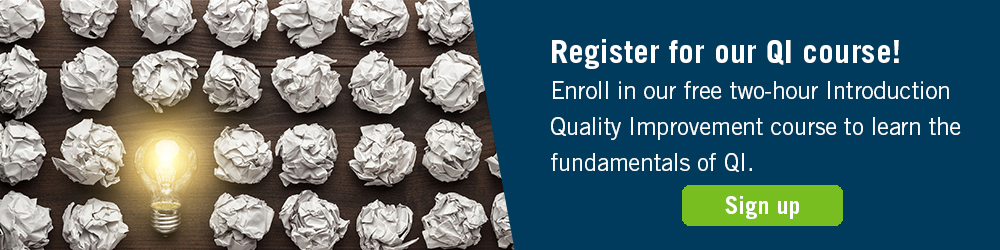